Table of contents
In the dynamic world of fashion, the advent of 3D printing technology has opened a realm of possibilities that once seemed the domain of science fiction. Imagine a future where the boundaries between imagination and reality blur, with fashion accessories customized to the finest detail and produced sustainably at the touch of a button. This exciting innovation is not just reshaping how accessories are designed and manufactured; it's revolutionizing the fashion industry's entire supply chain. As this technological marvel continues to evolve, it becomes increasingly pivotal to understand its profound effects on style, sustainability, and consumer culture. The following exploration delves into the transformative impact of 3D printing on fashion accessories, uncovering the nuances of this burgeoning phenomenon. Readers are invited to step into a world where the traditional methods of accessory production are being challenged, leading to a future that promises both style and substance. Let's embark on a journey to discover how this technology is not just changing the game but setting an entirely new standard for the fashion world.
```htmlThe Revolution of Accessory Production
The advent of 3D printing technology, or additive manufacturing, has radically transformed the landscape of fashion accessory production. What was once a realm dominated by mass production techniques has now shifted towards a new paradigm emphasizing customization and on-demand manufacturing. This evolution has brought forth significant enhancements in the speed at which fashion accessories can be produced, shifting from the lengthy traditional production cycles to rapid prototyping and manufacturing that meet consumers' growing demand for personalized products.
Sustainable accessory production has also seen a considerable boost from 3D printing technologies. By allowing designers to create items without the excess waste typically associated with traditional cutting and manufacturing processes, 3D printing contributes to a more environmentally friendly approach to fashion. Moreover, the capacity to produce intricate designs with additive manufacturing has unlocked new horizons in innovative accessory design. Designers can now conjure complex geometric patterns and structures that would have been prohibitively expensive or downright unfeasible with conventional methods. The integration of keywords such as "3D printed fashion," "customization in fashion," and "innovative accessory design" not only reflects the current trends but also underscores the disruptive impact of 3D printing on the fashion accessories industry.
```Personalization at the Forefront
In the realm of fashion accessories, 3D printing has emerged as a transformative force, bringing personalized fashion to the forefront of consumer-driven design. Through this innovative technology, individuals can now actively participate in the creation of their accessories, effectively blurring the lines between producer and consumer. This participatory process is often referred to as "co-creation," where customers provide input that influences the final product, thereby fostering a stronger personal connection with the pieces they choose to adorn.
Custom-fit accessories are no longer a luxury reserved for the elite; 3D printing personalization has democratized the ability for anyone to tailor items to their exact preferences. Whether it's selecting specific dimensions to suit their body type or incorporating elements that reflect one's individual style expression, 3D printing offers a versatile platform for personalization. Beyond aesthetics, the technology is also attuned to the functional needs of consumers, such as creating accessories that accommodate unique physical requirements, ensuring both style and comfort.
The integration of 3D printing in fashion accessories signifies a significant shift towards a more inclusive and consumer-centric industry. It empowers individuals to express their unique identities through fashion and, in doing so, transforms the traditional dynamic between fashion brands and their clientele. The impact of 3D printing on personalization is not just a fleeting trend; it's reshaping the future of how accessories are designed, produced, and worn.
Material Innovation in Accessories
The advent of 3D printing materials in the realm of fashion accessories has not only broadened the aesthetic possibilities but also heralded a new wave of material innovation. Designers now have at their disposal a plethora of unprecedented textures and finishes, bringing a fresh and customizable aspect to accessory design. Beyond the visual and tactile diversity, these materials are making significant strides towards eco-friendly fashion. A prominent example is the use of biodegradable polymers, which are carving a niche within the industry as biodegradable accessories begin to rise in popularity.
Such advancements are not merely cosmetic; they represent a tangible step forward in sustainable fashion technology. The incorporation of biodegradable materials is a testament to the industry's capability to pivot towards more sustainable practices. This shift is driven by a heightened awareness of environmental impact and a demand for products that align with a greener philosophy. In this context, biocompatibility becomes a technical term of increasing relevance, denoting the harmonious interaction between these novel materials and the environment. As fashion accessories evolve, the fusion of style, innovation, and responsibility continues to reduce the industry's carbon footprint, paving the way for a future where fashion and ecology coexist symbiotically.
Challenges and Limitations
While the integration of 3D printing into fashion accessory production has brought a wave of innovation, it is not without its challenges. One of the main hurdles facing designers and manufacturers is fashion production scalability. The current 3D printing processes can be time-consuming and less conducive to mass production when compared to traditional methods. This issue often leads to higher costs of 3D printing, as the technology is still evolving to meet the demands of large-scale manufacturing efficiently. Furthermore, there are also technology limitations; the machinery available may not be suitable for all types of designs or materials, which can stifle creativity and limit the application of 3D printing in the industry.
Notwithstanding these obstacles, the industry is actively seeking solutions to enhance the practicality of 3D printing in fashion. Efforts are being made to refine the technology to achieve economies of scale—the point at which the cost per unit decreases as production volume increases. This progress is crucial in making 3D-printed fashion accessories a viable option for mainstream markets. Additionally, ongoing research and development are aimed at overcoming production barriers such as improving the speed and versatility of 3D printers, expanding the range of wearable materials, and reducing overall costs. With input from experts like business strategists in the fashion sector and 3D printing engineers, there is a concerted push toward operational excellence, ensuring that the benefits of this innovative technology can be fully harnessed in the future.
The Future of 3D Printed Fashion Accessories
The trajectory of 3D printing in fashion accessories suggests a revolutionary shift, blending the lines between futuristic innovation and artisanal heritage. As we peer into the horizon of fashion technology, we envisage a landscape where next-gen fashion accessories become statements of both style and technological advancement. With the future of fashion technology unfurling before us, the industry is ripe for a surge in digital craftsmanship, a term that encapsulates the fusion of technology with the meticulous skill of a traditional craftsman.
Predictions indicate a burgeoning trend in personalization, with 3D printing paving the way for accessories that are not just tailored to, but co-created with the consumer. The integration of biometric data in design processes could lead to accessories that fit not just in style, but in ergonomics, revolutionizing comfort and functionality. This trajectory heralds a new era where the heritage of craftsmanship is not lost but reimagined; the tactile knowledge of materials and design principles is translated through the lens of cutting-edge technology.
As the 3D printing evolution accelerates, one might speculate that traditional accessory artisans will adopt new roles, becoming guides in a digital landscape, merging time-honored techniques with the limitless possibilities of 3D printing. The fashion world, adept at embracing the avant-garde, stands on the cusp of this integration, likely leading to a symbiotic relationship between the old and the new. In this dynamic future, the possibilities for innovation are boundless, promising to redefine our conception of what it means to accessorize in the 21st century.
On the same subject
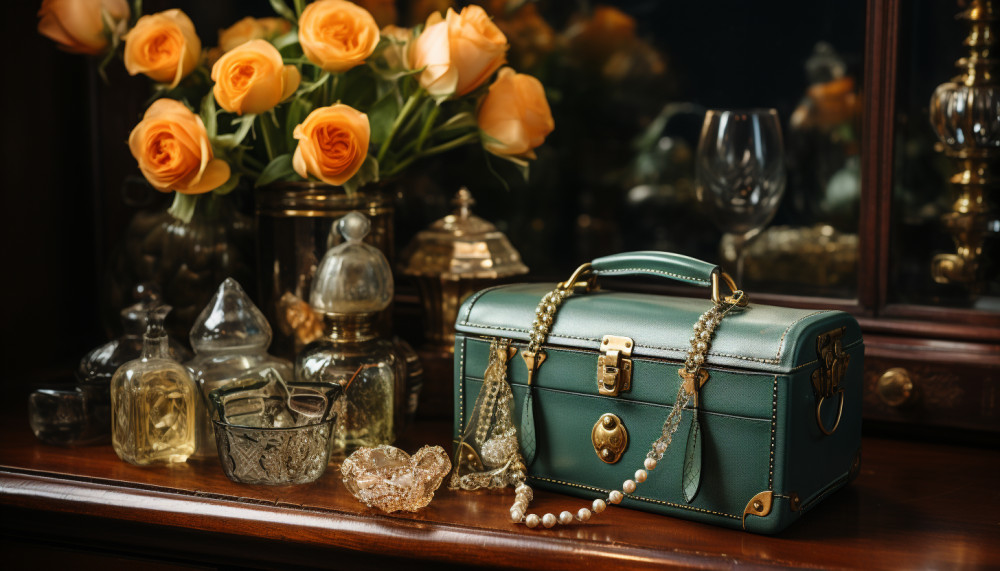
Unlocking the Mystery of Vintage Accessories
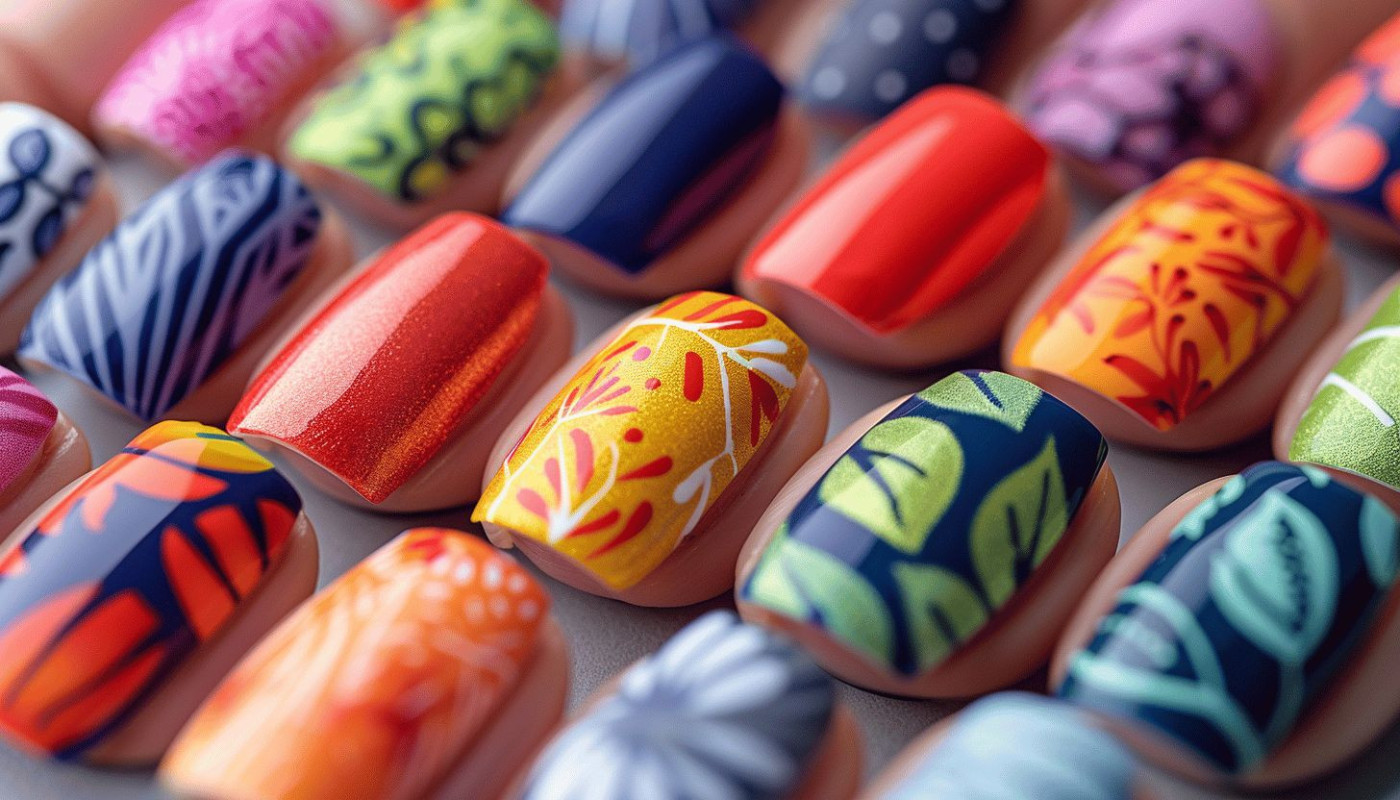
Exploring The Versatility Of Nail Wraps For Every Season And Style
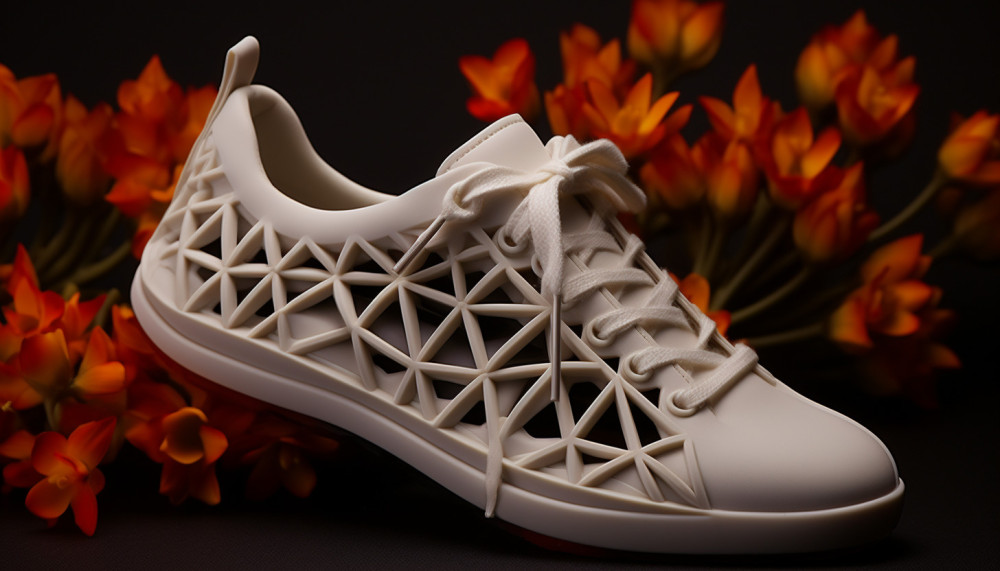
Exploring the Impact of 3D Printing on Fashion Accessories
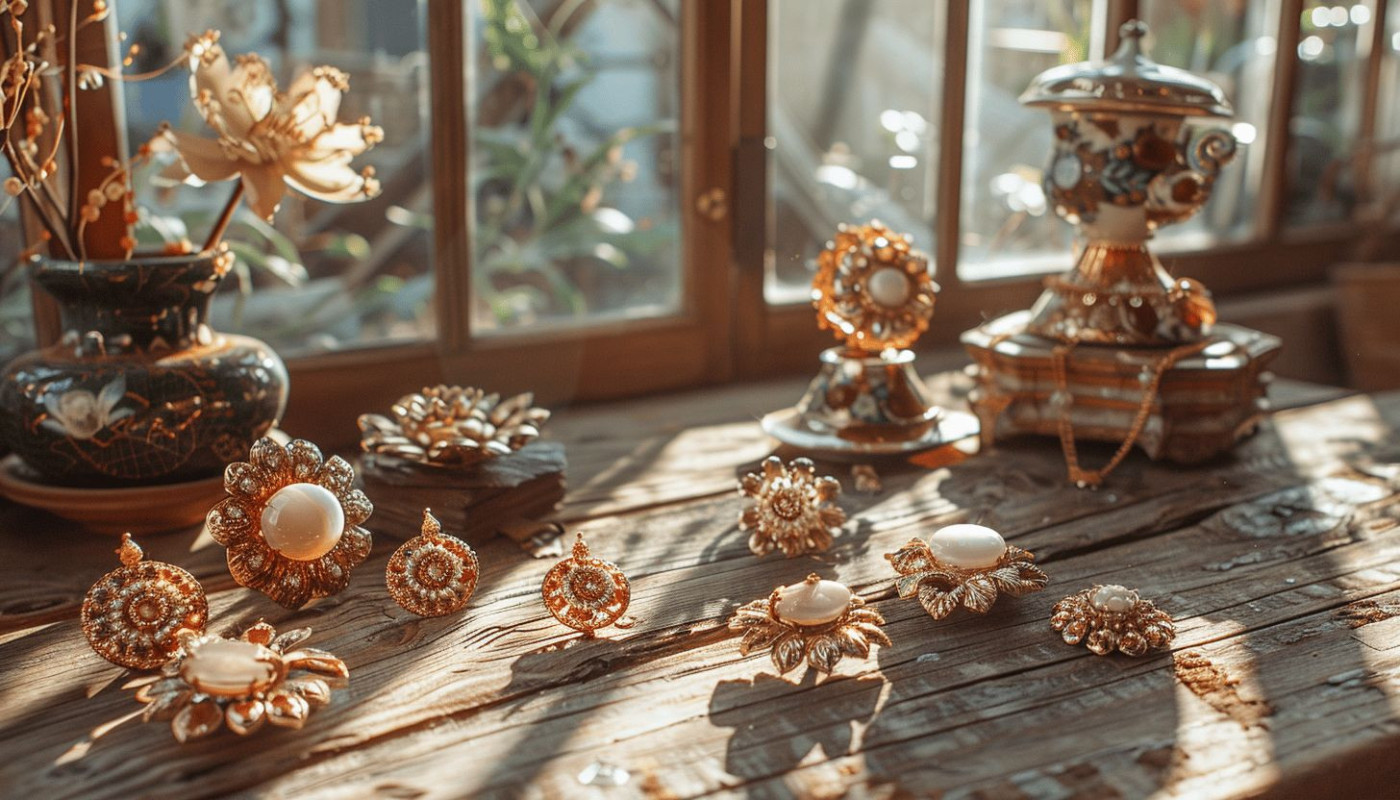
Crafting elegance how to style handcrafted jewelry for everyday wear
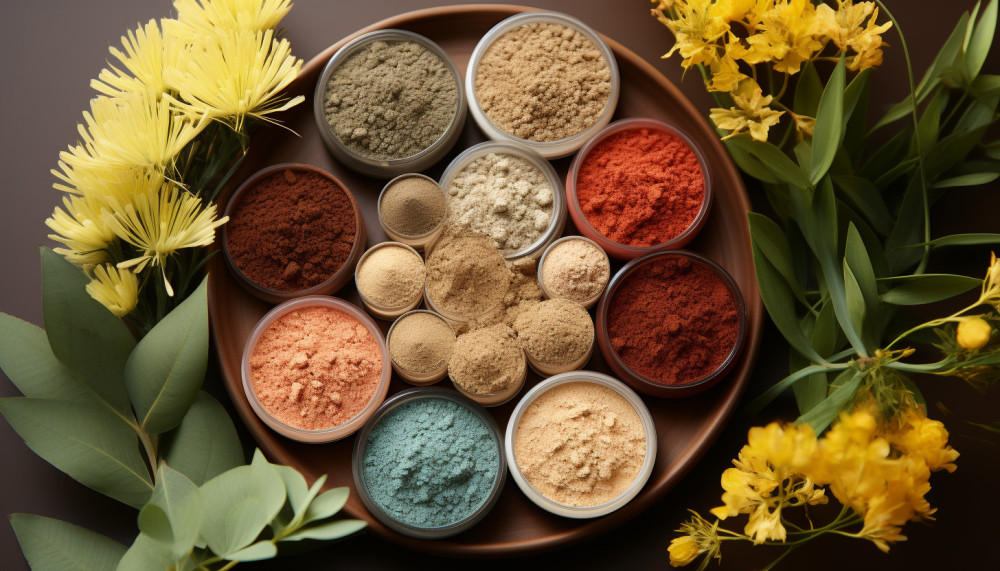